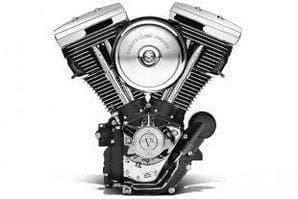
The Harley-Davidson Evolution engine is entirely new only from its base gaskets up, though the crankcase does contain significant refinement. What are the changes and their purposes?
First, an engine’s operating temperature is the balance between the heat the engine generates and the ability of its cooling system to reject that heat. Most heat is picked up through chamber and exhaust port walls from combustion gases, but some comes from bearing and piston friction. The hotter an engine runs beyond the capacity of its lubricants and cooling system to protect it, the shorter its life.
Previous H-D big twins had deep combustion chambers with two valves set at a 90-degree angle to each other. At the time of their design this was standard practice in the finest piston powerplants — large aircraft engines. The deep chamber was necessary to achieve the low six-to-one compression ratio needed then, and to give room for the very large valves that were then necessary for adequate airflow.
At the moderate horsepower level of 1936 this chamber was fine, but after the war, when available fuel octane rose, compression ratio and performance rose with it. Higher piston domes added even more surface area to the already excessive acreage of the deep chamber. At high power, this deep chamber and domed piston absorbed tremendous heat, robbing the combustion gases of energy that would otherwise have appeared as extra pressure on the pistons. As a result the cylinder heads ran very hot.
Moderate power
In engines of moderate power, iron is the logical cylinder material; it is strong enough to act as engine structure and provides an excellent low-friction surface for the piston to run against. When power rose after the war, the iron cylinder showed its limitations as a conductor of heat. Larger clearances kept the hot pistons from seizing, but this solution was inadequate. The hot piston, picking up heat in its crown from the combustion flame, can only rid itself of this heat through its rings and through direct, intimate contact with the cooler cylinder wall. With the large clearances, piston-to-wall contact was limited to two narrow strips in the front and back — too little to guide and cool the piston properly. Consequently the hot pistons frequently broke down the cylinder wall oil film, leading to rapid piston and ring wear. Smoking and loss of compression and power were the inevitable results.
These dire consequences followed from trying to extract more power from an older design with no basic engineering changes. The time had come.
Each cylinder of the Evolution engine has a very shallow combustion chamber with its two valves set at only 58 degrees to each other. With such a shallow chamber, the 8.5:1 compression ratio is achieved with a perfectly flat-topped piston — reducing the exposed piston area in the chamber to the mathematical minimum. This reduction in combustion chamber heat loss translates into a fat gain in torque at all engine speeds. Energy formerly lost as heat is now kept in the combustion gas and can assist in pushing the pistons down. This also translates into reduced cylinder head operating temperature — spark-plug washer temperature is down by 75 degrees F.
This new head is sand-cast in SAE 242 aluminium alloy, noted for its heat conductivity and stability at temperature. Although the H-D Staff wanted to die-cast the head, they could not because 242 is too viscous at pour temperature to completely fill a cool metal die before it solidifies.
In machining, a sensing finger gauges the depth of the cast chamber, controlling the depth of milling cuts which will determine the compression ratio. The HD cylinder head prodution line uses $3.5 million worth of new tooling — almost entirely automatic. The heads are, predictably, massive and substantially finned for air cooling.
Using their racing department’s knowledge of airflow, Harley’s engineers were able to supply this new head with more air through new, smaller valves and ports. If this seems wrong, then you should know that airflow specialists often recommend smaller than stock valves in certain racing engines — to increase performance! Another benefit of this valve-size reduction is a lower exhaust-valve temperature. In a small valve, the hot centre is closer to the cooler seat at the outer edge. As the hottest part in the chamber, the exhaust valve sets the upper limit on compression; too high, and the hot valve can make the engine detonate. Cooler parts in the chamber translate to a higher safe compression ratio, which in turn increases performance and reduces fuel consumption.
The new chamber is not truly a slice from a sphere; the side opposite the single spark plug is lowered to make a squish band against the piston’s flat top. Fuel economy as well as mid-range torque depend on finding ways to stir up the mixture before combustion.
Rapid combustion translates to low heat loss and good torque. At peak-power rpm, the velocity of the intake stream generates plenty of turbulence but the mid-range needs other means. Therefore, as the HD piston nears TDC, The mixture trapped between piston and head squish area squirts out in a jet, stirring up the chamber and promoting fast, turbulent combustion. The production tolerance on the thickness of this squish zone is 0.028 inch-0.043 inch. At highway speeds, this new motor can achieve 55 miles per gallon.
Very conservative
To improve drivability, Harley engineers kept valve timings very conservative. Longer valve timings, combined with tuned intake and exhaust systems, can produce impressive torque figures, but only over a limited range. Because the Evolution engine was designed to please touring riders who want to glide up hills at the crack of the throttle — not by stirring around in the gearbox and whining the engine up towards peak revs — valve overlap is at a low minimum. This, aided by porting that combines high velocity for ram effect with high mass flow, yields a broad power curve with its torque and horsepower peaks as far apart as possible. Between them is a wide zone of easy drivability; dial the power you need.
In place of the base-bolted solid iron cylinder of old is a new finned aluminium cylinder with an iron liner cast into it using a process called SpinyLok. Base-bolting, which in the past has allowed some cylinders to break right off, is replaced by through-studs in high-tensile steel. Since they are primarily aluminium, the new cylinders more closely match the expansion rate of the aluminium pistons, and clearance can be reduced almost to nothing. Tight clearances accomplish several things. First, they place the piston in much closer thermal contact with the cool cylinder, so the piston is itself well cooled. In fact, as the piston expands, it contacts the cylinder over a wider and wider area, cooling itself and automatically regulating its temperature and operating clearance. Second, tight clearances give a broad, supportive oil film between piston and cylinder, extending its life by cutting down on metal-to-metal contact. Finally, a tight piston clearance holds the piston more strictly aligned on the cylinder axis, presenting the rings to the cylinder wall at a true perpendicular so they can develop a good oil film and seal over the long haul. In factory tests, engines could be run at full throttle with as little as 0.0004-inch assembly clearance, but production clearance will be 0.0014.
With cases, cylinders, and heads all made of aluminium, heat expansion and contraction of parts will be similar. In the old design, where iron and aluminium met across a gasket, heating and cooling cycles made the dissimilar metals scrub back and forth across the gasket, literally wearing it out. The massive weight of the old iron cylinders also tended to make them “walk” on the case gaskets as the engine vibrated. Now steel locating dowels lock cylinder to case and head to cylinder to prevent any such excursions. The new cylinder can be rebored and fitted with pistons in four oversizes.
Although tight piston-to-wall clearance is an excellent beginning, it is not the entire key to long piston life. The pistons must be correctly contoured as well. Conventional oval pistons concentrate sliding contact at the back and front of the skirt, not at the sides. This prevents excessive friction. They also taper from top to bottom — smallest at the top to compensate for heat expansion, and largest at the skirt where conditions are much cooler. Unfortunately, this simple oval/tapered shape doesn’t make the best pistons because as a piston expands in use, it expands an extra amount where there is more material — over the massive wristpin bosses, for instance. To give a true cylindrical bearing surface against the cylinder wall at operating temperature, the cold profile of the piston must be the inverse of this irregular, hot, expanded shape. Knowing what this might be is a matter of experience and testing. Project engineer Don Valentine believes there are three first-class piston manufacturers in the world today, and that none of them is in the US. Harley’s new piston is made by Mahle, the German piston and cylinder specialist. It is cast on automatic five-piece permanent moulding equipment and then its complex surface contour is turned at high speed by a diamond cutting tool controlled by a three-dimensional cam. Added to the expansion contour is a slight inward taper at the bottom of the skirt to make this part of the piston act as a surfboard; the piston can ride up on the oil film rather than scraping it off. The pistons are cast in a low-expansion 12-percent silicon alloy and carry a barrel-faced chrome top ring and a conventional three-piece oil control ring.
Top-end oiling in the old engines was accomplished by leakage-prone external oil lines, but the Evolution engine sends its oil up automotive-fashion through one-piece hollow steel pushrods. The oil enters them from the hydraulic roller tappets at the bottom and discharges at the top into the drilled socket end of each forged-steel rocker arm. The arms are wide, pivoting on solid hardened pins in widely spaced plain bushings. The oil enters the space between the bushes, flows across to the valve side of the rocker, and squirts out of a small drilling to lube the rocker-to-valve contact.
Rocker and valve
Improper geometry between rocker and valve sometimes results in the rockers trying to overturn the valve as it lifts it. The guide then wears quickly and oil is drawn through into the combustion chamber, where it produces smoking on overrun. Bad geometry here often results when valve lift is increased without re-engineering of the position of rocker tip and valve stem. The new engine is carefully executed in this respect and its rocker tips are radiused and polished to induce a steady rotation of the valves. This tends to distribute heat evenly around the valves and seats, reducing warpage and leakage.
Oil pumped to the heads must have free return to the crankcase below or it will pool around the valve guides, making the engine smoke. Drillings in each cylinder at the low (exhaust) side drain the oil, and this would work just fine if gravity were the only force at work here. In a Vee-twin, a large change in crankcase volume occurs with every piston stroke. This huffing and puffmg interferes with the drain-back of oil, alternately forcing it upward, then hastening downward. The situation worsens if high head and cylinder temperature sludges up the drains with oxidised oil.
In the new engine, heads and case are kept at the same pressure by making the four pushrod tubes act as generous “equaliser tubes,” connecting through cored-out passages in the all-new tappet-guide blocks. Case and head pressures rise and fall together, leaving gravity to get on with the important work of oil return.
Serviceability was another major design goal. To get a low seat position over so tall an engine, the top frame rail must pass close to the heads. No one would tolerate an engine that had to be pulled from the frame for top-end service, so H-D engineers designed a multi-piece top-end assembly, each of whose elements was vertically thin enough to be slid out from under the frame. The rocker arms are not mounted on the head itself, but are set into a removable rocker frame, topped by a two-piece cover consisting of a spacer ring and cover plate. With the heads in place, the pushrods, pushrod tubes, and tappet assemblies can be removed for service. Though the engine is held together with the new through-studs instead of the old base-bolts, these studs rise only as high as the tops of the cylinders and end in female threads. This means the head secures to them by bolts.
Once these bolts come off, the heads can slide sideways off the tops of the cylinders. The studs are short enough that the cylinders can lift off them without hitting the frame above.
Each rocker frame bolts to its head with nine fasteners and sandwiches an automotive-style rubber-beaded gasket. The spacer ring and cover plate are sealed by rubber-impregnated gaskets held captive in grooves, much like big 0-rings. This prevents over-compression and extrusion of these gaskets, making a good, permanent seal. Four fasteners hold each spacer and cover down on its rocker frame. Top-end service will be quick work, a tribute to the incorporation of maintenance considerations in the design.
Towering Harley cylinders
The two towering Harley cylinders have always (except for the racers and the derivative XR1000) had their intakes in the vee, facing each other so they can be joined to a single carburettor by a Y-manifold. In the old design, the manifold connections had to be solidly screwed together, complicated because the heads were not positively located atop their cylinders. To assemble, you tightened the head bolts finger tight, then tried to make the manifold connections. The heads were pulled into whatever position the manifold demanded, and then you tightened the head bolts. Without locating dowels, engine vibration allowed heads to “walk” on their gaskets, making them leak eventually. As this happened, the connections to the Y-manifold loosened and leaked, affecting the engine’s idle.
In the fresh design, the Y-manifold is joined to each cylinder by a bonded rubber coupling and clamp like those used on millions of other machines. This accommodates all misalignment, seals positively and permanently, and permits the heads to be positively located so their gaskets stay healthy.
On the exhaust side, leakage at the exhaust coupling and even outright falling-off of the pipe were problems. The earlier rigid-mounted engines had a lot of movement between the pipe and head; loosening was only a matter of time. The rubber-mounted Evolution engines have their pipes carried on a “nodal point” (a point of zero movement) on the frame in a rubber bushing. The engine and its pipes now move as one, eliminating the relative motion that formerly loosened the pipes. The exhaust gasket is a porous metal-fibre part which crushes down at installation, then fills solid with carbon in use to effect a solid seal. Pipe leakage is stopped.
The H-D big twin has used roller tappets for many years, but increased loads from stronger valve springs and higher average speeds have caused occasional problems with roller surface damage. Surface failure in rolling contact can be banished by increasing the radius of curvature, so the Evolution engine has tappet rollers of increased diameter. In place of the complicated three-piece H-D hydraulic lifters (which were originally, in 1948, located at the tops of the pushrods) are automotive-style hydraulic tappets. And why hydraulics at all? An engine this tall, made of aluminium, expands some 0.018 inch in warm-up. Without some automatic compensation scheme, cam timing would shorten with increased temperature, and the engine would be noisy.
Valve-train stress depends not only on the weight of the parts and the speed of operation, but also on the nature of the cam profiles. Years ago a mathematically simple profile, easy to plot and to machine, used to be the first choice, but such profiles produce sudden changes in acceleration which can break parts.
Valve springs are set into vibration, with waves of compression bouncing back and forth between retainer and spring seat, which quickly fatigue and break the spring. Valves can hit their seats with enough force to bounce up again.
The Evolution engine uses more complex polynomial cam forms which limit the rate of change of acceleration to controlled values. Experimental cams were designed, ground, and then rig-tested under a strobe light to determine their stability. As a result, the big twin now has a valve train stable out to a thousand rpm beyond the point at which the rev-limiter circuit begins to operate.
Detail changes to the lower end carry the load of future development. Like all H-Ds, the Evolution engine is a roller motor, with its rear rod’s big end forked to allow the front rod to fit into it on the three-row roller crankpin. A fork-and-blade rod configuration like this places the cylinders one directly ahead of the other, not slightly offset as they would be if the rods were side by side. The result? The engine vibrates purely in a single plane, with no twisting. Where the front rod is cut out for the rear there were formerly many stress-raisers. To permit the rods to clear each other and the mouths of the cylinders, they must have a curious cranked outline which also produced stress concentrations. The new design uses rods whose fatigue strength is ten times that of the old ones.
The original crankpin was lubricated by an oil hole that emerged in the centre of the front rod’s roller track. The stress of rolling contact, particularly in the more powerful new engine, could cause chipping and spalling from the edges of this hole. It has therefore been moved to an unloaded zone under one of the roller cage separator rings. Dimensionally, the cages which guide the rollers have tightened up. This ensures more nearly perfect rolling, rather than skidding contact. The crankpin’s surface has also been improved.
The big twin has been brought up to date and yet it remains recognisably a Harley-Davidson engine.